We offer tailored solutions based on comprehensive system and process expertise from extrusion technology to feeding and bulk material handling for pharmaceutical and nutraceutical processing requirements.
Pharmaceutical
Coperion and Coperion K-Tron are experienced partners for the pharmaceutical and nutraceutical industry
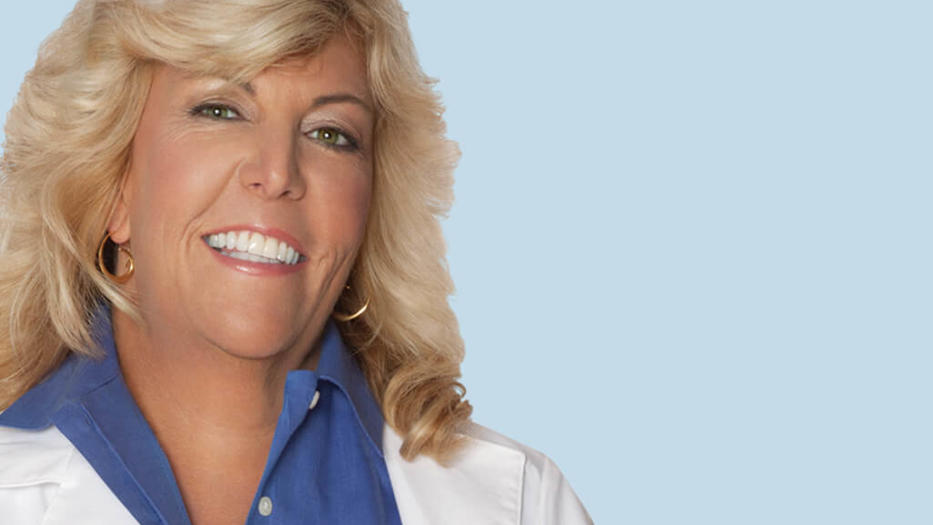
Years of experience makes us ideal partners for handling even the most challenging pharmaceutical applications.
Sharon Nowak , Business Development Manager Food & Pharma Applications
Coperion and Coperion K-Tron can provide single source solutions for all of your extrusion, feeding and conveying needs in the pharmaceutical and nutraceutical industries. Our complete line of equipment is engineered to meet the rigid requirements of the industry, including strict adherence to cGMP guidelines and standards as well as the use of FDA approved materials of construction. Our expertise in processing even the most difficult to handle excipients and active ingredients has resulted in global recognition of our equipment and engineered services, with a particular strength in providing continuous processing solutions. Our partnerships with pharmaceutical and nutraceutical companies of all sizes continue to grow, resulting in specialized technical solutions with an emphasis on product and process quality.
Now with Coperion Food, Health and Nutrition Division we can offer even more specialized equipment and technologies for these industries. Our brands include Coperion K-Tron, Diosna, Gabler Engineering, Unifiller, and VMI. Learn more about Coperion Food, Health and Nutrition Division.
Comprehensive Product Range
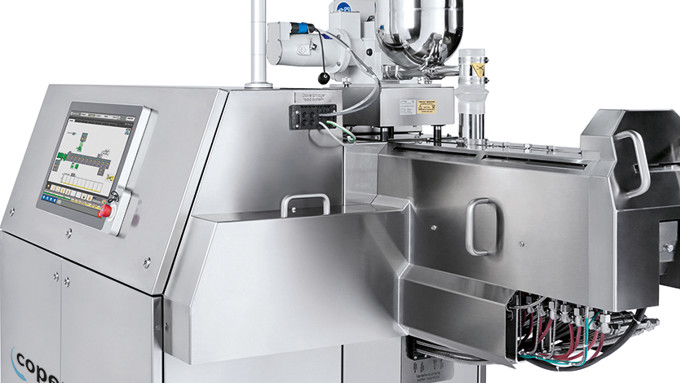
Pharma Extruders
High-end twin screw extruders for pharmaceutical applications
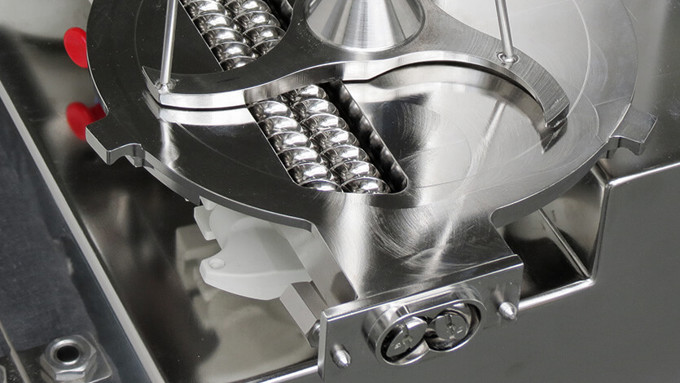
Process Equipment
High quality equipment for all pharmaceutical processes - from feeders to valves, hoppers, bins, etc.
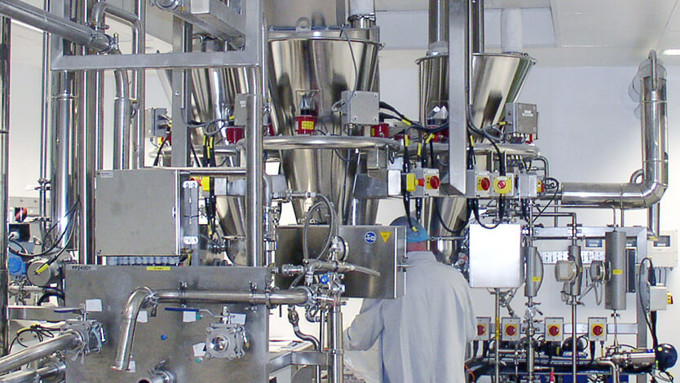
Plants & Systems
Outstanding total solutions for all industries
We offer expertise in a wide range of pharmaceutical and neutraceutical applications
Coperion K-Tron contributes feeders to new Pfizer CMT
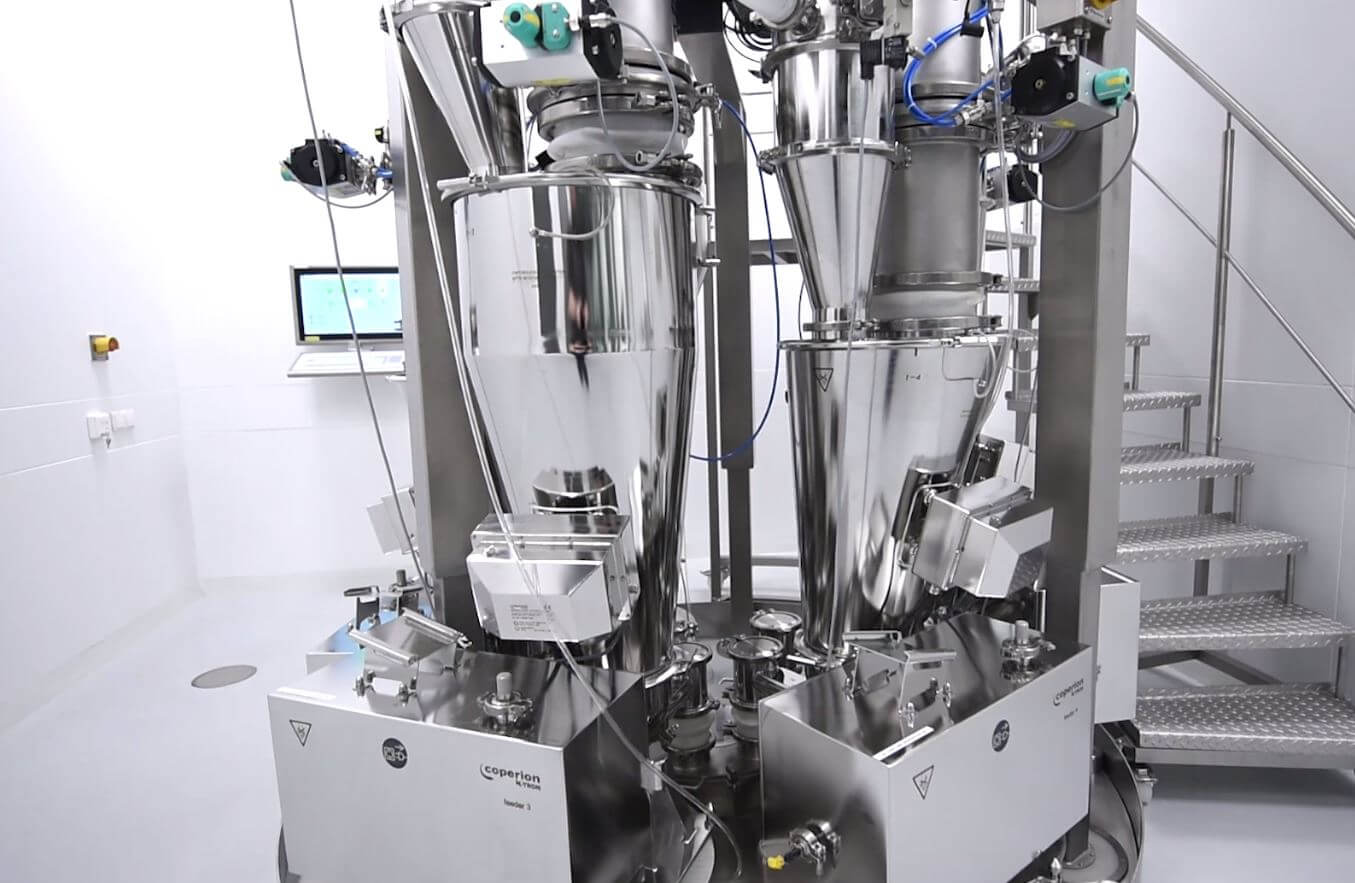