Batteries are taking on more and more significance in our increasingly digitalized and connected world. At the same time, they are crucial for advancements in certain industries and areas such as electric vehicles. To keep up with these fast-moving developments, cost pressures and environmental concerns, manufacturers of batteries are looking into more cost-efficient production processes. Switching from a traditional batch process to a continuous production set-up is known to offer a range of advantages.
Infographic: Switching to a Continuous Extrusion Process when Producing Battery Masses
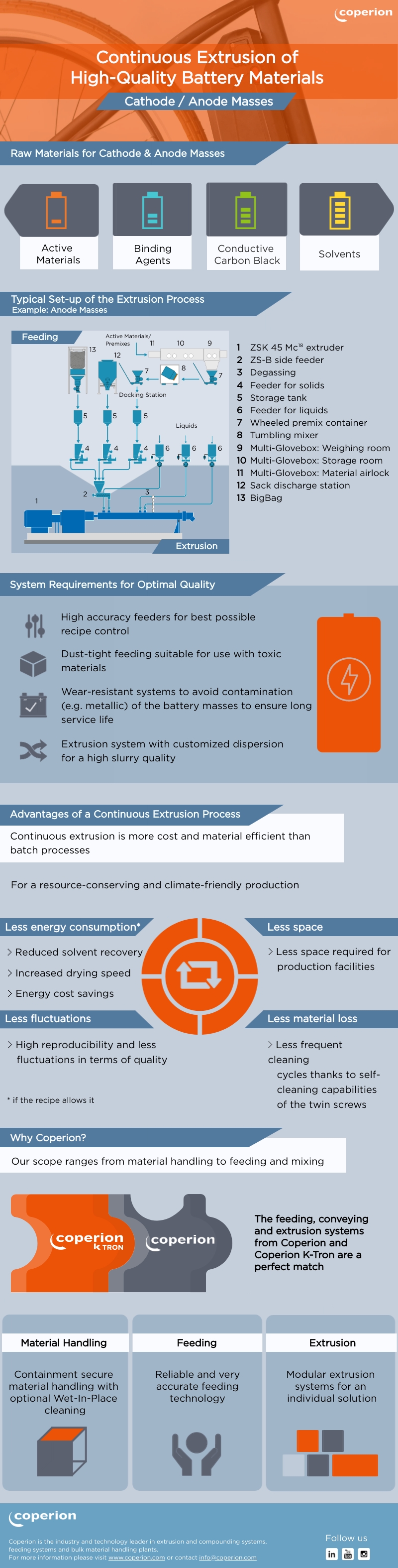
The continuous extrusion process is suitable for the manufacturing of cathode/anode masses, which are the heart of a battery and thus one of the biggest cost drivers. As the infographic shows, raw ingredients for battery masses include active materials, binding agents, conductive carbon black and solvents. To make sure that the battery masses and end product meet the desired quality level, the production set-up has to be designed around an optimal interplay between feeding and conveying systems as well as the extruders. All (toxic) materials need to be fed in the exact amount, at the exact time and in a safe environment. Therefore, high accuracy and reliable feeders are important for optimal quality as they allow for maximum recipe control. At the same time, the feeding equipment needs to be dust-tight and suitable for toxic materials. The wear-resistance of systems is also an extremely important factor since it avoids contamination of the mass (e.g. metallic) and ensures a long service life of the battery. Another equipment requirement which has an impact on the quality level is the process section of the extruder itself. Each product is different and therefore the extruder should support customized dispersion as it again increases the slurry quality.
But what are the advantages of continuous extrusion in comparison to batch processes?
Generally, a continuous production set-up is more cost and material efficient which automatically leads to a more climate-friendly production. If the recipe allows it, it is possible to lower the energy consumption. This is possible due to reduced solvent recovery, increased drying speed as well as energy cost savings as a result of a more efficient production line. Moreover, less space is required in the production facilities which again translates into a reduction of the overall project costs. The continuous process also has a positive effect on the slurry quality as there are less fluctuations in the mixing process thanks to a higher level in reproducibility. In addition, less material is lost as twin screws extruders are known for their optimal self-cleaning capabilities. As a result, less cleaning cycles are required.
The feeding, material handling and extrusion systems from Coperion and Coperion K-Tron go hand in hand and ensure an optimal interplay between these process steps. Based on decades of experiences in various industries, we provide contained material handling solutions with Clean -in-Place and Wet-In-Place cleaning options, highly accurate feeders and modular extrusion systems to meet individual process challenges.
Download the infographic
Learn more about Coperion's solutions and capabilities
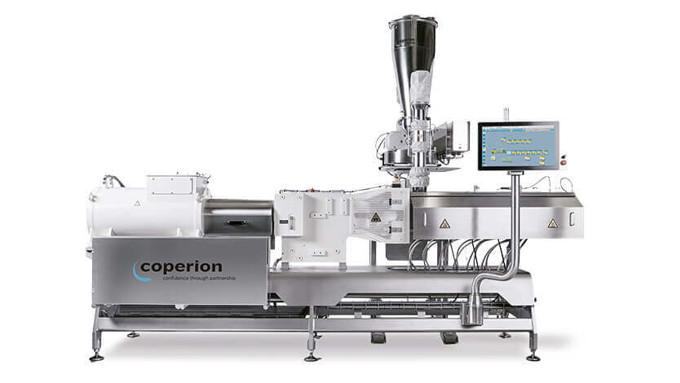
Producing Battery Compounds
Coperion provides ideal feeding and extrusion technology for producing a wide variety of battery components. The focus is on the continuous production of electrode materials and separator films.
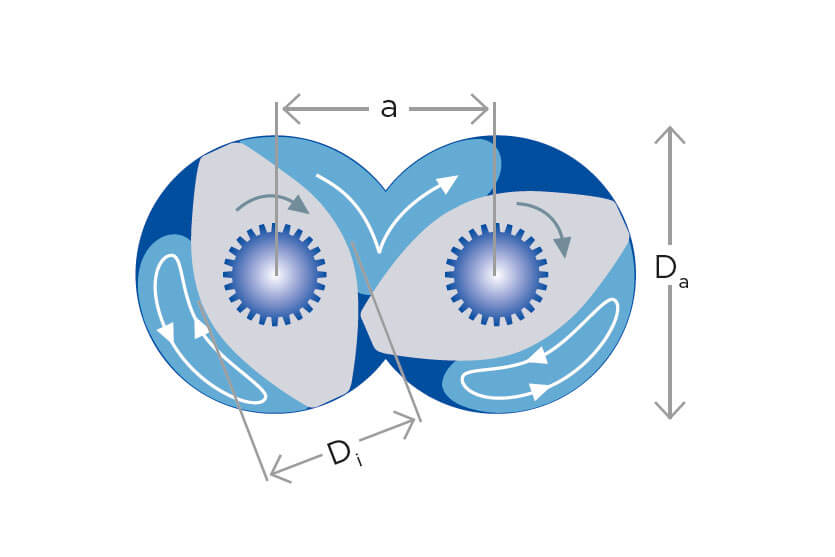
Extrusion Technology
As a pioneer in the development of the closely intermeshing, co-rotating twin screw extruder, we possess unique know-how and an extraordinary wealth of experience in this field.
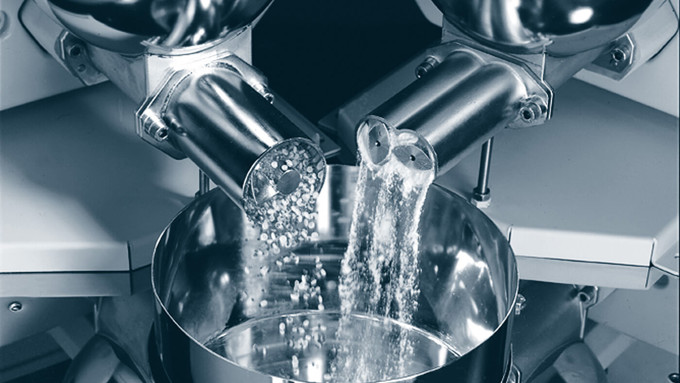
Smart Feeding Solutions
No two process applications are the same, and Coperion K-Tron offers the widest range of feeding solutions in the industry.