Coperion K-Tron has recently launched a new line of K3 vibratory feeders based on a unique pendulum technology. As a result, the material at hand is not only fed more accurately and gently but the system also proves to be significantly more efficient. How such an improvement in efficiency may affect purchasing decisions can be seen in the following infographic:
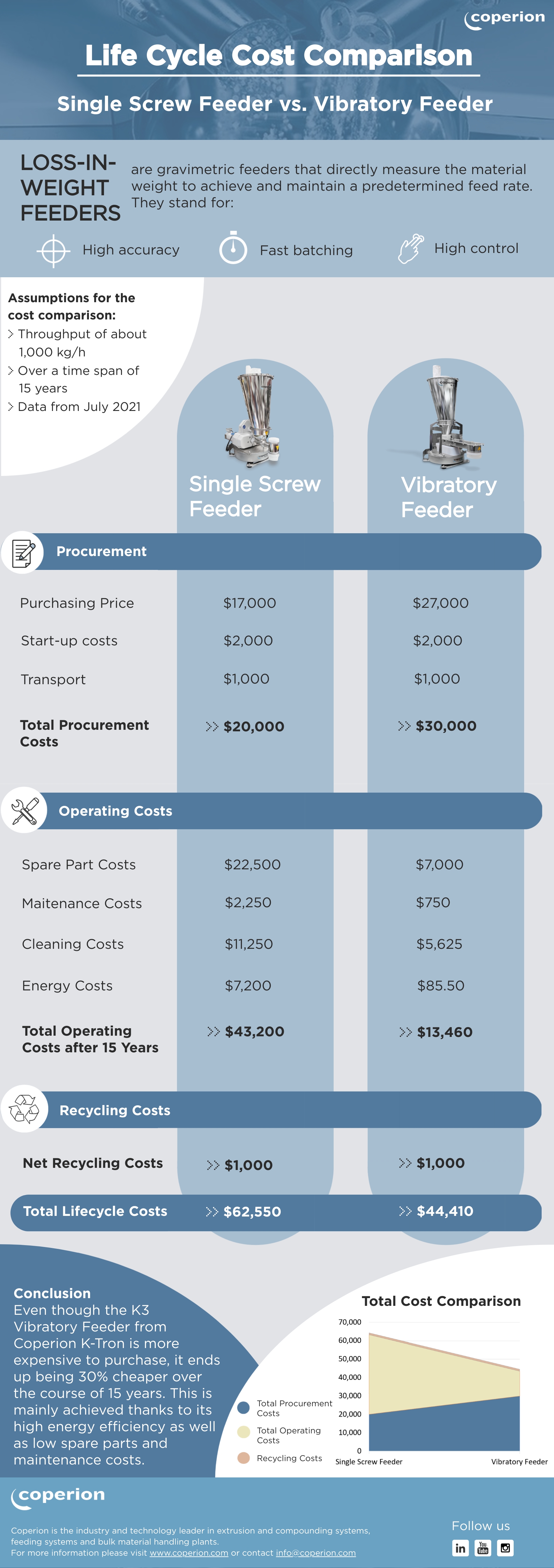
To begin with, the procurement costs of the new vibratory feeder are 1/3 higher than a single screw feeder. This is in part due to the unique technology. Therefore, screw feeders seem to have an initial cost advantage when only looking at the purchase price. When taking the operating costs into account, calculations show a completely different picture. Contrary to single screw feeders, the new vibratory feeder has hardly any wear parts as a result of which spare part costs are non-existent. Over a life time of 15 years, it can be expected that a single screw feeder requires spare parts worth $1,500 per year resulting in overall spare parts costs of $22,500 after a life time of 15 years. The vibratory feeder on the other hand usually does not require any replacement of parts. Nevertheless, this does not preclude that the drive or measurement technology need to be updated in the course of its life time. It may also make sense to opt for a state-of-the-art control unit at some point so as to be able to benefit from additional optimizations in the future. Overall, it can be assumed that costs associated with any updates of the vibratory system amount to $7,000. At the same time, maintenance and cleaning of the vibratory feeder tends to be less time consuming. The K3 feeder is especially designed for quick cleaning and along with its lack of wear parts, bi-annual maintenance is limited to a scale check or calibration. Therefore, the K3 vibratory feeder maintenance and cleaning costs amount to only $6,375 in the course of 15 years. The cost advantage of the vibratory feeder also becomes evident with regard to energy usage. Thanks to its innovative drive and advanced control system, power consumption is just a fraction of the energy usage of a single screw feeder. The vibratory feeder can be operated at 0.019 kilowatts when feeding at a throughput rate of 1,000 kg/h whereas the single screw feeder uses a 1.6-kilowatt motor. On the basis of the assumption that both systems are in operation for 2,500 production hours per year and energy costs 12 cents per kilowatt hour it can be concluded that the energy costs of a single screw feeder is 85 times higher than those of a vibratory feeder. This cost advantage becomes even more relevant when production is located in countries with high energy prices. In the end, total operating costs of a vibratory feeder are $13,460 over its complete life time. The single screw feeder however can be expected to reach expenses of $43,200 after 15 years.
After adding up all of the costs, the K3 vibratory feeder is the clear winner in this sample calculation. While the single screw feeder’s life cycle costs come to $62,550 the vibratory feeder only generates $44,410 in expenses. Therefore, in many cases the vibratory feeder is indeed the better choice – both from a cost and from a product perspective.
You are interested in the details of this cost comparison? Read the article from our newsletter here.
Download the infographic
Learn more about Coperion K-Tron’s feeding equipment
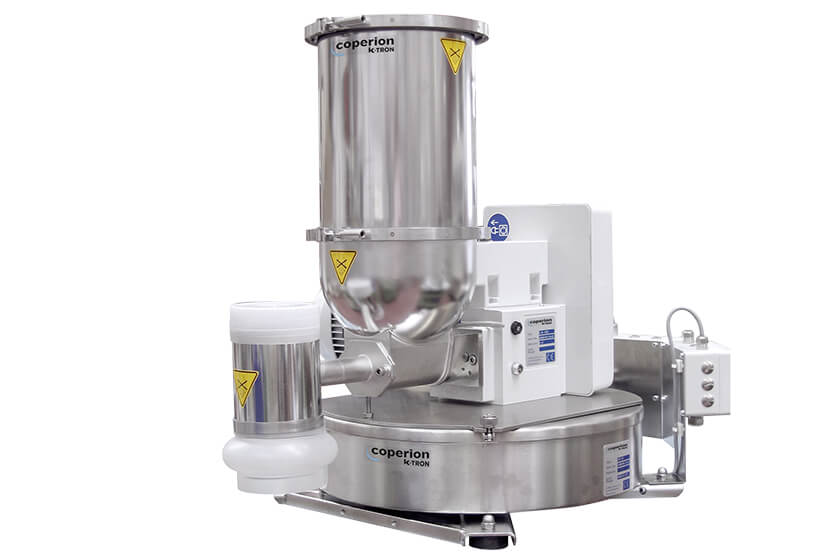
Single Screw Feeders
Reliable feeding of free-flowing bulk materials - Single screw feeders are ideal for feeding free flowing bulk materials such as pellets and powders.
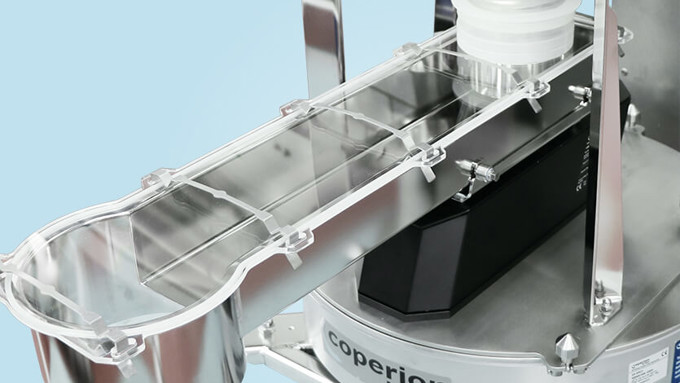
Vibratory Feeders
Vibratory feeders are ideal for gentle handling of a wide range of bulk solid materials, especially fragile ingredients.
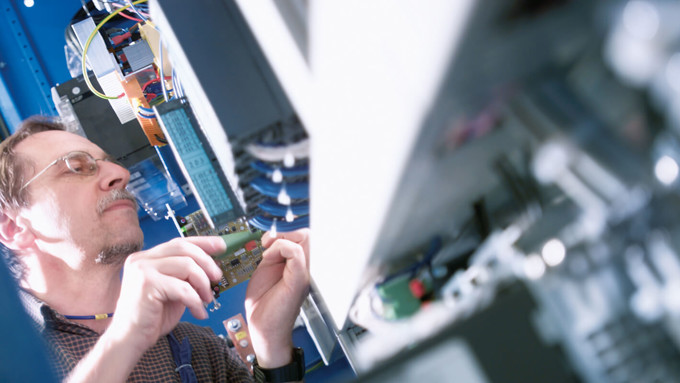
Feeder Modernization
Benefit from Coperion K-Tron’s latest feeding technology to improve your product quality and extend the life of current equipment.