Niederlenz, Switzerland (April 2023) – Coperion K-Tron announces the expansion of the original ProRate™ PLUS feeder portfolio with more solutions for feeding powders. A ProRate PLUS-MT twin screw feeder will be added to the product line that will be available end of April 2023. Together with the recently introduced ProFlow™ bulk solids activator the new twin screw feeder is an efficient solution for feeding powder additives in plastics applications. Last year Coperion K-Tron developed a completely new feeder line built on 100 years of feeding experience to provide a robust and reliable feeder for simple feeding applications in the plastics industry. The ProRate PLUS continuous gravimetric feeder line is an economical solution and offers a quick return on investment due to its good price-performance ratio and fast delivery times. The original product line featured three single screw feeders that are ideal for the feeding of pellets, granules and other free-flowing bulk materials in secondary plastics applications.
Coperion K-Tron Expands ProRate PLUS Feeder Line with twin screw feeder for powder additives
Preconfigured Feeders for Plastics Industry
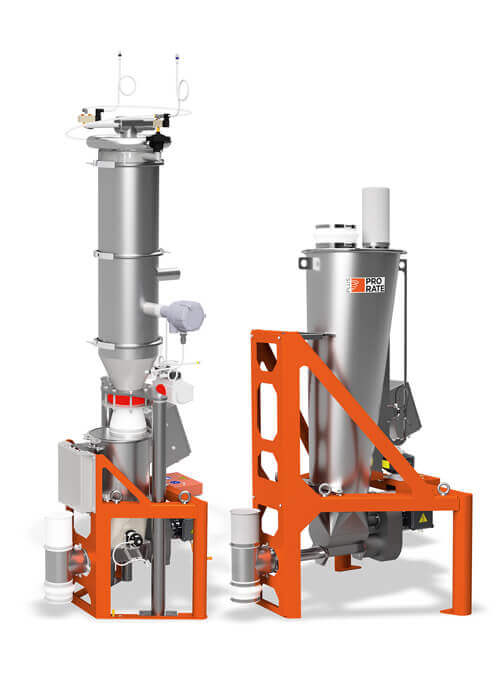
New twin screw feeder ideal for powder additives
For more difficult to handle materials Coperion K-Tron is expanding the ProRate PLUS product line with a new twin screw feeder, the PLUS-MT. This gravimetric feeder with its horizontal agitator ensures that the two screws are always optimally filled with material. The twin screw technology also has the advantage of reducing pulsations and the screws have a self-cleaning effect. Twin screw feeders are ideal for difficult to handle powder additives such as talc, calcium carbonate or carbon black. The steep design of the hopper walls allows poorly flowing bulk solids to be fed reliably without an additional vertical agitator. Should material bridging or ratholes still occur, one or more ProFlow bulk solids activators can be mounted on the hopper to promote material flow.
The new ProRate PLUS-MT twin screw feeder can handle throughputs from 40 up to 1800 dm3/h [1.4 to 63.6 ft3/h], depending on bulk material characteristics. With individual bulk solids tests in our test centers, we can determine more precisely what the exact feeding range is for a specific bulk material.
Controlled vibrations improve feeder performance
Together with the new ProFlow™ solution, the scope of the original ProRate PLUS single screw feeders has been expanded to include moderate flowing powders and flakes. The solution is available for all four models (PLUS-S, PLUS-M, PLUS-L, PLUS-MT) and can be installed on new equipment or as a “mounting kit” on existing feeders.
The ProFlow bulk solid activator consists of an electromagnetic vibrating device, which activates the feed hopper to keep bulk materials moving. The device operates at an optimized frequency and amplitude to ensure minimal energy consumption and maximum product flow. Thanks to its smart electronic control, ProFlow only uses 3.6 Watts of electricity. Tests with a wide range of bulk materials have shown that ProFlow is an ideal solution for a variety of bulk materials. ProFlow has no wear parts and since it is mounted outside of the product contact area, there is no additional cleaning effort needed.
For the smaller PLUS-S model, the ProFlow activator is implemented in conjunction with specially developed overflight screws. Overflight screws have wings that help move the bulk material into the throat of the feeder and positively promote improved screw fill.
Clever design features for ease of use
The ProRate PLUS feeder line features a space-saving trapezoidal shape which allows up to six feeders to be easily grouped around an extruder inlet within a 1.5 meter [5 ft] radius. The four feeder models PLUS-S, PLUS-M, PLUS-L and PLUS-MT cover a wide range of throughputs. The ProRate PLUS feeders are capable of handling feed rates from 3.3 up to 4800 dm3/h [0.12 up to 400 ft3/h], depending on the material. Theoretically, a feeding system with six ProRate PLUS-L feeders can feed up to 28.8 m3/h [1017 ft3/h] on a footprint of only 7 m2 [75 ft2].
ProRate feeders are highly standardized and include a variety of design features to optimize performance and ease of use. Simple access for cleaning and maintenance, even within a cluster, is provided thanks to a patent-pending rail system called “ProClean™ Rail”. ProClean Rail makes it possible to retract the base unit toward the rear of the feeder and rotate it for access to the feeding section and screw element while keeping the feeder in position. In addition, the bellows and screws use the latest magnet technology for simple but robust mounting. The magnet connections allow these parts to be released without tools while at the same time providing the required holding force for optimal and safe operation.
Thanks to the high level of standardization of the feeders, the number of spare parts required for an emergency stock is minimal. Many parts are identical for all three models and can be used as exchange parts for all devices.
All ProRate PLUS feeders are equipped with P-SFT load cells, featuring reliable Smart Force Transducer single wire weighing technology. Each feeder also comes equipped with its own pre-wired and pre-tested ProRate PLUS PCM control module. The PCM is mounted to the feeder stand, with adjustable height positioning. Most feeders only need a basic motor control unit (PCM-MD) while one feeder per group of eight is equipped with an advanced version featuring an integrated user interface and line control functionality (PCM-KD).
ProRate PLUS feeders and the ProFlow bulk solids activator are suitable for use in hazardous locations rated NEC Class II, Div. 2, Group F & G and ATEX 3D/3D (outside/inside).
Preconfigured refill packages for continuous material supply
Preconfigured pneumatic refill solutions are available for each feeder size. Each feeder can be outfitted with either a filterless vacuum receiver for pellet applications or a vacuum receiver with a cartridge filter for applications where there may be dust that must be kept out of the air only line of the vacuum conveying system. Refill solutions include a compact support stand, level indicators, butterfly valves and electrical terminal boxes as well as one or more vacuum blowers as needed. The Series 4 MPC controller is ideal for up to 24 vacuum receivers on one blower with one back-up blower.
Downloads
Contact
-
Regula Sullivan
Marketing Communications
- email: regula.sullivan@coperion.com
- telephone: +41 62 885 7314