For those of you currently implementing continuous processing into your production, many are aware that consistency and accuracy in the feeding of the API(s) and excipients are key criteria in ensuring a high quality final product. In many cases, the traditional excipients used for the same product in batch processing may not be ideally suited for a continuous process due to poor flowability. Today’s excipient manufacturers are actively pursuing methods to reformulate or co-process some of these traditional excipients. As stated by David R. Schoneker Chair of QbD/Composition Committee – IPEC-Americas, “As CM becomes more common, excipients that have been traditionally used may not provide optimal CM formulations. The need for new excipients has never been greater, nor the benefits clearer. Novel excipients with improved properties can enable API solubilization, consistent product mass flow, more precise PAT measurements, and in some cases, better pharmacokinetic profiles with improved dosing regimens and higher product efficacy.“
Sign up for the Coperion newsletter to receive the latest updates
Feeding Excipients to Continuous Processes
What are the new developments in formulation and equipment design to improve flowability?
In many continuous processing applications, the loss-in-weight (LIW) feeders are considered the “heart” of the process. Improved flowability of the materials through these feeders will not only improve end product quality, but will also help in overall process efficiency and minimizing downtimes. In response to this important requirement, Coperion has worked very closely with several key excipient manufacturers to test new formulations as well as educate on the specific requirements of optimal loss-in-weight feeding. Our Global Business Development Manager, Sharon Nowak, has recently been involved in three important presentations/conferences specific to this important topic. These presentations included the following:
- Co-Presentation with IFF at the AAPS conference of a poster entitled “Impact of Microcrystalline Cellulose Particle Size Grade on LIW Continuous Feeding”
- Presentation to IPEC – Americas (International Pharmaceutical Excipients Council of the Americas ) entitled “An Equipment Manufacturer’s Perspective on Excipient Considerations for Continuous Manufacturing”
- Presentation at the recent CMF (Continuous Manufacturing Forum) entitled , “Impacts of Material Flow Properties on Continuous LIW Feeding and How to Overcome These Challenges”
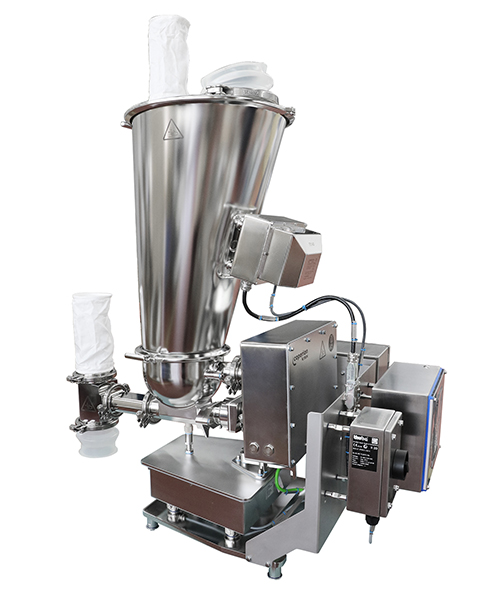
All of the presentations above include specific examples and comparisons of how LIW feeder accuracy can be improved by reformulation, “design for purpose” and equipment modification techniques. In addition, further in-depth discussions are being held regarding improving additional flow issues by co-processing certain excipient combinations. This practice of pre-blending certain poorly flowing API’s, for example, has been practiced by some companies for some time simply by silicating the API with SiO2 and then introducing the blend to the LIW feeder. Since API’s are generally known to be inherently poorly flowing due to their typically micronized particle size and high aspect ratios, pre-blending with the SiO2 has been known to help with overall flow.
In addition to excipient reformulations, the presentations above included further mechanical innovations by Coperion to help with feeder performance and address additional challenges in a continuous application which are often overlooked, such as consistent feeder refill. Flow aid devices such as the patented Coperion K-Tron ActiFlow smart vibration technology, as well as improved and automated feeder venting solutions are easily implemented solutions to some of the flow issues in both loss-in-weight batch dispensing and continuous dispensing applications.
For further information or copies of any of the presentations mentioned above, or for further details on how Coperion can help to improve your batch dispensing or continuous processing applications, including hot melt extrusion, wet extrusion, continuous direct compression, continuous wet or dry granulation or continuous coating , please do not hesitate to contact us!
Your Contact
-
Sharon Nowak
Global Business Development Manager Food & Pharma
- email: SNowak@coperionktron.com
- telephone: +1 856 256 3119
- Sharon Nowak on LinkedIn Profile