Salina, KS, August 2023 – At this year’s Battery Show North America (September 12-14, Novi, MI at the Suburban Collection Showplace), Coperion and Coperion K-Tron will present their innovative technologies and total solutions for continuous manufacturing of battery materials. At Booth 3227 visitors can learn about the advantages of this efficient manufacturing process and how Coperion delivers complete high containment systems for the continuous production of battery masses. Solutions from Coperion and Coperion K-Tron span the entire process of anode and cathode slurry production, from intake, conveying and preparation of the active materials, to feeding and mixing in the extruder, to material handling of the finished masses to further processing.
Advanced Technologies for Continuous Production of Battery Masses
Coperion and Coperion K-Tron at The Battery Show North America 2023.
Safe conveying and feeding for processing active material and black mass recycling
Proper processing of the active material plays an important role in battery compound manufacturing. Since the active material is fundamentally responsible for energy storage in the battery, precise manufacturing of this material is essential for high-end product quality. The active material is manufactured in a multi-step process that relies upon both safe handling and accurate feeding of bulk materials and additives. Coperion’s conveying systems, as well as Coperion K-Tron’s feeders, are used for the safe transport and high accuracy in feeding ingredients. The same holds true for black mass recycling. Due to the use of hazardous materials in active cathode material manufacturing, as well as in black mass recycling, secure containment is essential. Coperion conveying components, with their dustproof design and gentle handling of abrasive bulk materials, are among the most impressive features for manufacturers. Coperion K-Tron high-accuracy, reliable feeders are suitable for safe feeding into the process, thanks to state-of-the-art weighing and control technology which ensures that the active material is manufactured under protected conditions at a high level of quality.
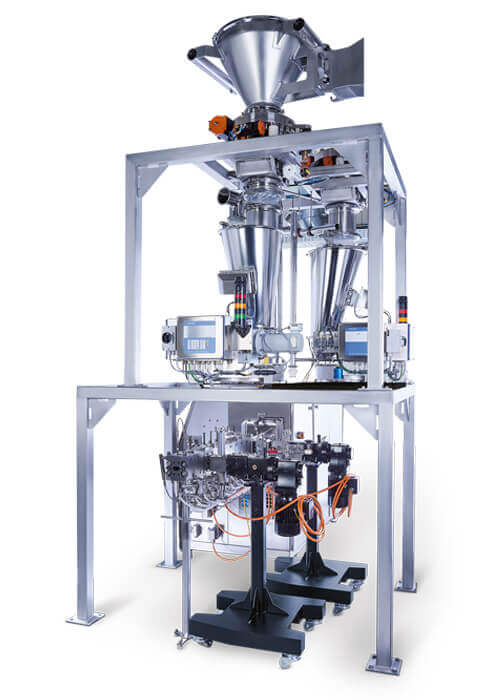
Semi-Dry or Dry Process: Continuous battery compound production with twin screw extruders and loss-in-weight feeders
Using twin screw extruders and loss-in-weight (LIW) feeders as essential components in continuous processes provides battery manufacturers with a highly efficient method of production. With the ZSK Mc18 twin screw extruder, Coperion offers the ideal solution for high reliability, profitability and meeting the highest demands for quality and throughput in battery compound production. Due to the extruder’s high torque, both semi-dry and dry processes can be realized using this manufacturing process. The individual process sections within the extruder allow for mixing of dry masses, thus smoothing the path toward future forms of processing. In comprehensive tests, battery compounds have already been successfully manufactured on Coperion extruders using Coperion K-Tron feeders in both semi-dry and dry processes.
With Coperion K-Tron feeders even the most difficult to handle materials can be accurately fed, on a short time basis, consistently, providing incredibly high tolerances for the raw materials being added, giving outstanding control of the recipe formulation. This can be achieved using the right feeding technology, single or twin screw, vibratory or other specialized feeding tool, combined with the high resolution SFT load-cells, rapid sampling times, 450/sec, and fast response of the KCM control systems, up to 50/sec.
For recipe development, Coperion provides efficient solutions using the ZSK 18 MEGAlab and the ZSK 26 Mc18 twin screw extruders. These laboratory and small-series extruders are designed for the demands of research and recipe development, and are ideally suited for testing new, expanded or modified recipes as well as for validating them. These extruders provide high performance even at the smallest batch sizes, making short, quick trials possible. Both models have been developed based on proven ZSK technology, ensuring reliable production-level scale up. The complete system is constructed as a space-saving unit — the feeders are mounted on a rack above the extruder and the control cabinet is integrated in the extruder base frame, allowing the laboratory machine to be installed even in the smallest space.
Recipe management of materials is handled through Coperion K-Tron LIW feeder KCM controllers. Each ingredient receives a mass-flow setpoint, all of which can be coupled using a line controller (K-Vision) into a Line of materials, each running at a proportion of other. In this way the rates can be linked, changed and tracked to and against each other. A variety of refill solutions are also available.
Extrusion, feeding and conveying systems for battery materials are available for testing, allowing you to ensure the characteristics and functions of the equipment.